August 9, 2023: Rattle Battle 3
Sonic resonance has reached maximum amplitude and the ship can't take it anymore!
- Montgomery Scott, probably
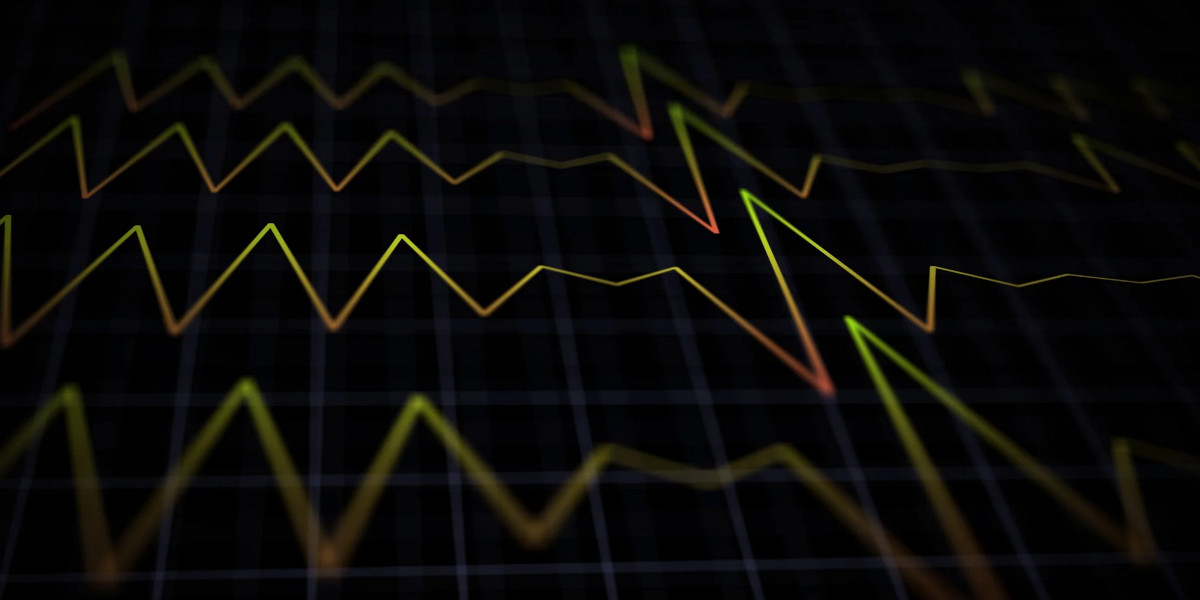
A few more hills to climb.
It's the last 20 percent which consumes 80 percent of the effort. Almost 2 weeks after I started on this de-rattlization project each progress increment has felt like I was getting close to the finish line, only to realize after a test drive or two that there are more gremlins lurking beneath. Each time I iron out one wrinkle, another surfaces. An iterative, tedious, frustrating, trial-and-error-driven process betraying the previous victory. As soon as I eliminate one rattle another immediately crops up like weeds, although each round of elimination makes the remaining creaks more distinct and somewhat easier to zone in on while chasing ghosts.
Having pulled out nearly every interior trim piece by now it's quite maddening how much of this could've been solved at the factory by buffering pieces/surfaces with basic padding material, although understandably all that adds cost and complexity to the design and manufacturing process. But to touch and rub your skin on some of these hard plastic parts ... yep, definitely not a Bentley. It's unfortunate that so much additional custom work is required to make the car feel silent as it should be. For a long time the German-brand fan boys looked down on Tesla fit and finish quality and rightfully so. As Han Solo might say, the early Model S eventually sound like "a bucket of bolts."
But I think I've finally reached an acceptable finish line. It's not a flawless victory with zero rattles, but it's significantly better than when I started. It's almost as if I have a brand new car again, although only because of the new car sound, not the smell. And less rattle chatter means less fatigue to the senses and less overall psychological irritance.
Trunk Hatch
I finally gave in and attacked the rear hatch area. This involves removing all four trim pieces around the rear window starting with the top, then sides, then finally the lower hatch trim. I was not looking forward to this one as I had worked on this big piece once before a while back. It can be done by one person but it's preferable to have two. Since I didn't have the premium audio option I only had a couple of wire harnesses to disconnect before I could assess the amount of work needed.
Three of the blue push pins were crushed by my previous attempt at getting this large trim piece back onto the hatch frame. Good thing I bought some extras beforehand.
Prior to removing the trim I carefully outlined the edge of each trim piece with painter's tape to trace out where I needed to create a "gasket" using 1/4" strips of foam.
It's astonishing just how many areas needed treatment and I wish I had bought much more foam material to almost blindly cover everything to save some effort. There were loose wiring harness ends which were merely taped next to the metal frame, the trunk latch pulley cable was resting directly against the outer body panel (no doubt magnifying that rattle point over shaky ground), the various wires in the tail light assemblies were crossing each other and could emit rattles during bumps, loose push pins, large plastic surface areas where dangling wire harnesses could bounce against, etc., etc. I spent several hours combing through this area and treated both the metal frame and the trim pieces to virtually ensure nothing could create rattle points again, although there was one wiring harness mounted to the far rear of the hatch frame that had a slightly loose socket that I couldn't reach.
Putting the large trim piece back onto the hatch frame was not fun, but not as arduous as expected. The side pieces were a bit of a pain because I had additional push pins break on the rounded backsides and using the prying tool wasn't working very easily to pop them out for replacement. These things are definitely not user-friendly so I just left them as-is even though one trim piece didn't snugly fit back in as it should. I wish old-fashioned screws were holding the trim in place.
One area I almost completely neglected was the bottom sill trim and the side pieces next to it. It turns out that their edges are in direct contact with the body panel underneath and this is a notable transfer point of road vibrations. Applying some 1/8"-thick foam to various contact points muted a lot of the remaining rattling that was trumpeting its solo while on rough pavement. In addition some of the push pins involved for these parts were also jiggly and loose.
License Plate
After a test drive proved that the hatch-area rattling hadn't completely disappeared, I determined that the two foam strips I had applied to the back of the license plate years ago weren't enough. The original factory license plate frame was also a contributor to the sonic mess since the plate wasn't firmly in the frame. In the end I decided to buy a new four-screw frame to start fresh and cover the entire plate backside with foam as well as line the inside of the frame with foam so the plate is cushioned against every possible surface. With the original two-screw frame the bottom part would always potentially jiggle against the body panel during bumpy roads since by design it just hangs there somewhat loose.
On poorly-maintained freeways (I'm looking at you, 880 N) the ride would generate enough tire noise howl at the right frequency to create juuuuust sufficient resonance hum to rattle the back hatch so that the rear end of the car sounded hollow. Instant cheapification of your futuristic, state-of-the-art, bleeding edge electric car.
B-Pillar Seat Belt Guide D-Ring
The seat belt feeds into the B-pillar through an opening via a plastic bezel (part 1019450-00-A). Right behind this trim is a metal D-ring which the belt slides through and as you pull or loosen the belt from different angles this D-ring pivots sideways/forward/backward as the belt retractor in the bottom of the B-pillar maintains tension. The D-ring was knocking against this trim and while the clunking sound was subtle, it has become noticeable as I've slowly silenced other interior noise.
I partly muted this with a spare felt pad (literally one of these cut into two) and carefully applied them on the D-ring where it slides against the inner part of the plastic bezel. I couldn't use foam here since the ring needs to slide around to accommodate belt movement. Admittedly not an attractive solution, but it's not something I can see unless I shine a flashlight in there.
Center Stage Complete
Foam-lining the side panel trim pieces of the center console towards the front end as well as the arm rest piece helped substantially, but I decided why not do the side pieces next to the seat backs as well as the vent. And the vent was really tedious work, but it was worth it. Lightly bumping my hand against the center console now produces almost no discernable creaking noise.
Door Panel Gasketing
For the hundredth time I removed all four door panels and created a gasket-like lining where the edge of the door card could potentially rub against the painted metal (and based on scuffed areas on the paint surface this is likely what happens). So at this point there is no way in hell those edges could ever bump against bare paint, ever again. Ever. And yes, this made a remarkable difference for me.
Frunk
While not directly exposed to the interior cabin, the frunk trim had loose areas causing certain ends to bounce against metal panels. The lip next to the fender panel was apparently originally held in by plastic clips which of course after all these years had either partially failed or completely broken off. This resulted in paint that wore off, exposing the primer underneath.
Bravo for excellent design, Elon, chief architect of the Model S.
No doubt in my mind that these factors into the noise orchestra so I decided to remove all three panels, gave them a quick wash, then applied 1/8"-thick foam to the backside on the areas where I knew made contact with other parts. It never occurred to me that the frunk could be a source of rattles, but here we are. No prisoners.
Roof Crossrail Bow Trim, Headliner
The centerline which splits the glass roof into two is the crossrail which is covered on the inside by a plastic "bow" trim (part 1039464-02-C). Rattles which might be coming from the headliner area are extremely difficult to isolate while you're in the driver's seat and the vehicle's in motion, but if you manually wiggle this cover you can tell there's some play and could be the source of some noise. This cover's held in place by four push pins and I buffered various contact areas with 1/8"-thick foam. Most of the push pins were also loose and immediate candidates for tightening their seating. Instead of foam I tried using bits of felt and this seems to work just as good, if not better.
For the headliner I gently pressed against different sections and wherever there were little creaks or noises I inserted felt between the headliner and the roof frame.
And Two Tedious Weeks Later...
A LOT of labor went into this project and involved a lot of precise foam cutting to fit into tight interior locations while working in a small, dimly-lit garage without studio lighting. If I had ordered a ton more foam to apply large swaths at a time it might've made it slightly easier, but this still required creating custom shapes for every trim piece. And I originally thought this project would only need a few days worth of work, tops. How naive I was. In hindsight I probably should have had a more comprehensive approach rather than spot-patching bits here and there.
While it's not perfectly silent, it has gotten relatively close. I barely get the kind of rattles I started hearing two weeks into my ownership back in 2014. I skipped some areas like the headliner due to the level of work required for removal and the seeming minimal return-on-investment. I'm willing to tolerate faint distant rattles or light noise on occasion since this is a 9-year old car and restoring a quiet cabin to this degree is a major undertaking in my pursuit to keep the vehicle feeling mint. It's actually fun to drive again and bad pavement is of little concern to my senses. My car's equipped with the standard coil suspension (not air) so there's no exterior mechanical cushioning from road bumps.
Tools and Other Stuff Required for the Job:
Trim removal tools
https://www.amazon.com/gp/product/B000LNBLTK
Car Clips Fastener Remover Tool
https://www.amazon.com/dp/B09KGJVM2Q
Push pin/retainer clips for 9mm hole (Telsa part 1025401-00-A equivalent)
https://www.amazon.com/dp/B07QWFT7WD
Push pin/retainer clips for 8.5mm hole (Telsa part 1011813-00-A equivalent)
https://www.amazon.com/dp/B07QXDTY2B
1/8" neoprene closed cell foam
https://www.amazon.com/gp/product/B07WVQF1DF
1/16" neoprene closed cell foam (this is more commonly used, get a few rolls worth)
https://www.amazon.com/gp/product/B07WNS3XM4/
Felt ribbon (available at crafts stores, Amazon example linked; I only used for the vent lever and very little of it at that)
https://www.amazon.com/dp/B08G4HNVYJ
Felt sheet (available at crafts stores, Amazon example linked; I only used for one of the doors and headliner)
https://www.amazon.com/dp/B08T7LLYCP
Scissors
Patience. Lots and lots of patience.
NSFW language in the garage.
Videos I Referenced:
How to take apart a Tesla Door (Rich Rebuilds)
Telsa Model X/Model S dash and storage trim replacement (Escargot Garage)
Fixing Tailgate/Liftgate Rattle on Tesla Model S (Rado Trenciansky)
Tesla Model S Driver side Upper & Lower B pillar replacement (Tesla DIYDr)
Tesla Model S dashboard removal (RS Team Bulgaria)
Removed top dash pad of Tesla Model S (Rich Rebuilds)
Tesla Model S Yacht Floor Removal Instructions (EVANNEX)
Tesla Model S NVX Sound Upgrade / Installation Video (EVANNEX)
Tesla Model S Rear Hatch Locked Fix (Technoz Ski)
Tesla center console disassembly to tighten armrest bolts (David Glennon)
How to: Upgrade back-up Camera in a 2014 Tesla Model S (JoeMartinMVC)
In case you want/need to swap out your arm rest decor on a Tesla Model S/X (Ammar)
Center Console Upgrade for First Gen Tesla Model S (Backshop Electric)
There were several more but in my fury to get through this project as quickly as possible I neglected to bookmark them.
Summary of Fixes
Area | To-Do List |
Doors |
- Ensure all push-pins are snug. - Create 1/4"-wide foam lining where door card edge meets paint. - Apply foam to contact areas between door card and push pins meet (including the metal pins on the top edge of the door along the window) as well as the openings for the 10mm and T30 screws. - Apply foam lining to door frame where loose wiring harness, etc. could jiggle against. - Wrap loose exposed harnesses in a felt and tape down as needed. - Wedge/insert 1/4" strips of black felt into the areas where the arm rest pad meets the rest of the door card, perhaps add very thin strips of foam as a follow-up. - Wedge/insert strips of felt between the outer layer of the armrest pad and the inner side under the aluminum door pull trim; this requires wedging the trim removal tool along the edge to pull it outward a bit. - Apply 1/16"-thick foam to the backsides of the plastic door inserts covering the T30 screws. - Remove speaker grills, apply foam to potential contact points with the door cards. - Remove bracket where the window switch mounts into, remove switch (small Torx bit), apply 1/16"-thick foam where the switch housing fits in and also on the four poles where the bracket mounts to the door card. |
Trunk/Hatch |
- Ensure all push-pins are snug. - Create 1/4" lining where all trim edges meet paint. - Apply 1/16"-thick foam to contact areas between wiring harness/other and trim/hatch frame meet. - Check the trim pieces on the outer edge of the hatch (next to liftgate struts) to see if any foam cushioning is necessary. - Apply 1/8"-thick foam lining on sill trim and adjacent trim on outer edge where it contacts the vehicle frame, also apply on any other contact areas where it braces against the frame. - Apply 1/16"-thick foam on contact area between the sill trim and adjacent trim. - Apply 1/16"-thick foam on the liftgate pull cups. - Pry open the end of the trunk latch cover and apply foam where the two halves meet (this may not apply to Model S newer than 2014). - Remove speaker grill mesh on the large hatch trim piece, apply 1/16"-thick foam or perhaps use thin felt to buffer between it and the large trim piece. - Check trunk latch pull cable to see if foam may be needed to buffer between it and the metal hatch surface. - Check tail light wiring to see if they cross and might "bounce" against each other during bumpy rides. - Look for anything else where loose pieces may contact a plastic or metal surface. |
Frunk |
- Check for looseness on all main large trim pieces, removing and foam-line with 1/8"-thick foam as necessary. |
License plate |
- Create a barrier between license plate and frame with 1/16"-thick foam. - Ensure the backside of the license plate and any remaining exposed areas of the frame which faces the hatch surface is covered with 1/8"-thick foam. |
Dash |
- Remove the covers on each side of the dash, cover the inside with foam, felt-wrap the wiring harness that hangs loose next to the key fob antenna. - Remove the lower dash trim covers (note: driver's side is held in place with a T20 screw on the bottom) and line completely with 1/8"-thick foam. - Pry the top dash pad upwards and insert foam along contact points with the dash frame underneath (no need to completely remove the pad). - Pry off the binnacle cover inserted into the underside of the dash pad (cover sits directly above the instrument cluster screen), line with 1/8"-thick foam end-to-end; the edges in particular could rattle against the dash protrusions behind it. - Optional but may be necessary if you're brave: remove the decorative trim (comes in various finishes such as the carbon fiber) and remove the vents held in place by two T20 screws. Apply 1/16"-thick foam carefully behind the trim as well as between vent housing and trim panel. Note - may be a tight fit. - Check glovebox for any looseness which imply shaking of parts while on rough roads. |
Center Console |
- Remove rear trim piece below the rear vent, then remove the side pieces and line all inside contact areas with foam. - Pull off the armrests and pry the top decorative trim piece and line with foam. - Remove rear vent, remove face piece from vent housing, then carefully apply thin foam layers/pieces at different contact points. |
Cubby (beneath MCU) |
- Two screws hold the upper/lower halves of the cubby bin together - line all contact areas with 1/16"-thick foam. - Line the area facing the dash (rear of the cubby) with foam. - Consider tying down the diagnostic connector that hangs loose behind the cubby bin underneath the MCU. |
A-Pillar |
- Pry open the plastic cover (labeled "air bag"), remove bolt/washer, lift off top end of the pillar trim, cover all contact areas between trim and contents of pillar with foam (lower end of the trim should already have padding material). - Insert foam piece in the trim cavity where bolt/washer inserts into. |
C-Pillar |
- The trim piece in the hatch area that sits next to/above the parcel shelf can be pulled out and all contact points with adjacent trim should be lined with foam. - The trim piece next to the rear seat bolsters may be difficult to remove, in which case wedge small strips of foam or felt along contact points of adjacent surfaces. |
Rearview Mirror Housing |
- Remove the front piece, then the rearview mirror by twisting counterclockwise at the mirror base, then remove the main plastic housing piece. Line each plastic piece with thin foam at contact points and along almost all exposed areas. |
Crossrail Bow Trim |
- Apply foam or felt along different contact points between the crossrail bar and the trim. - Tighten down the push pins with foam or felt. - The trim hangs from the crossrail bar with plastic suspenders - surround these with felt and tie in place with tape. |
Headliner |
- Press around different sections of the headliner looking for odd sounds, then wedge felt or foam (without adhesive). |
The war is finally over, albeit with some battle scars. World peace has been restored. Perhaps I even increased the car's market value by $20. No passenger can comment now on how it sounds like a hollow tin can of ball bearings. One cannot ninja when the floorboard beneath you squeaks.
It reminds me of the heady days of Sputnik and Yuri Gagarin when the world trembled at the sound of our rockets. Now they will tremble again at the sound of our silence. The order is: engage the silent drive.
- Captain Ramius